
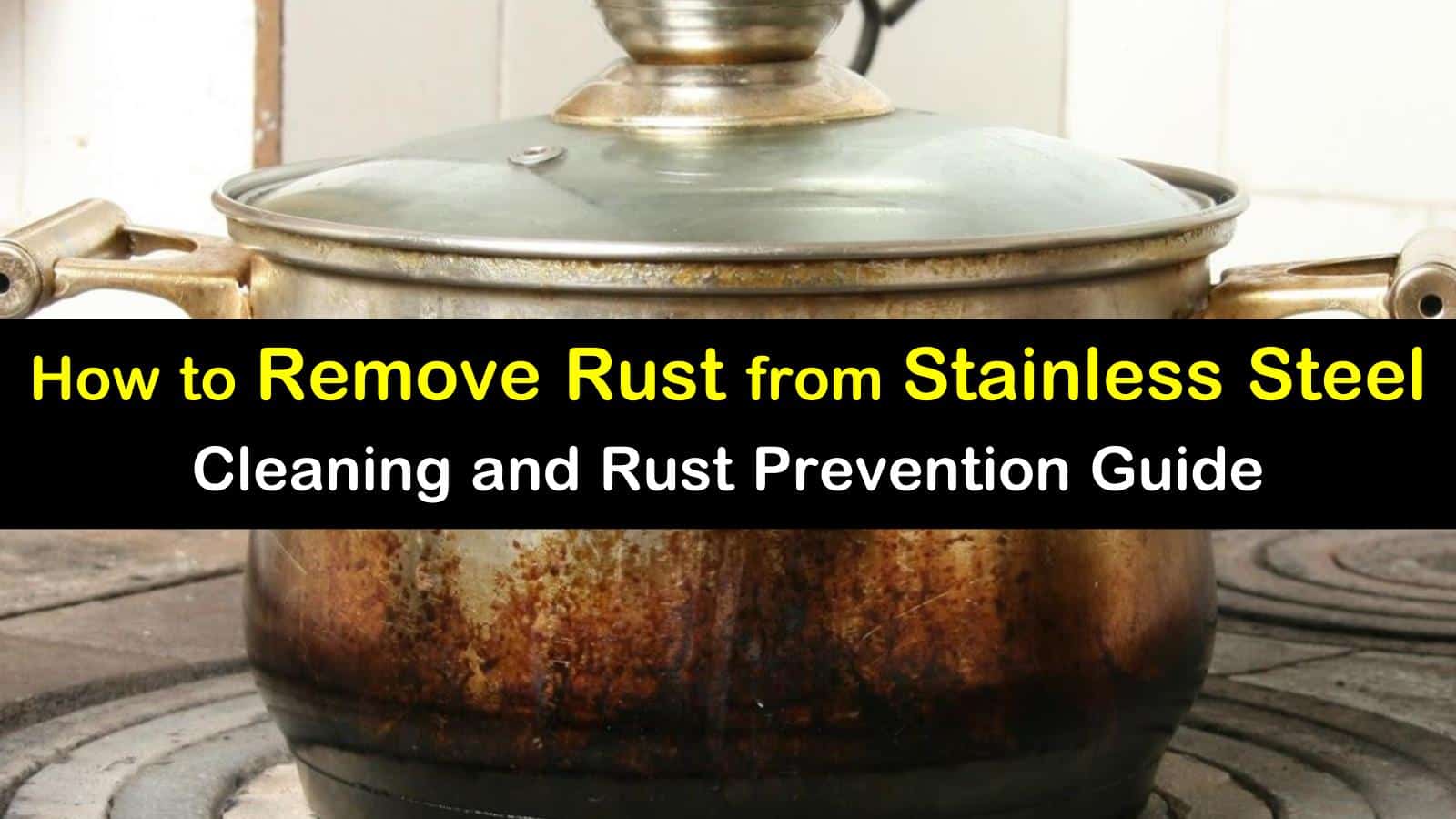
The difference between 304 and 316 stainless steel is the incorporation of molybdenum of 316 reaches up to 3%.
#Does 316 stainless steel rust series#
So its degree of corrosion resistance is higher than the 18-8 series stainless steels. The 316 stainless steel has 2-3% molybdenum added. So it must be hardened through cold working.
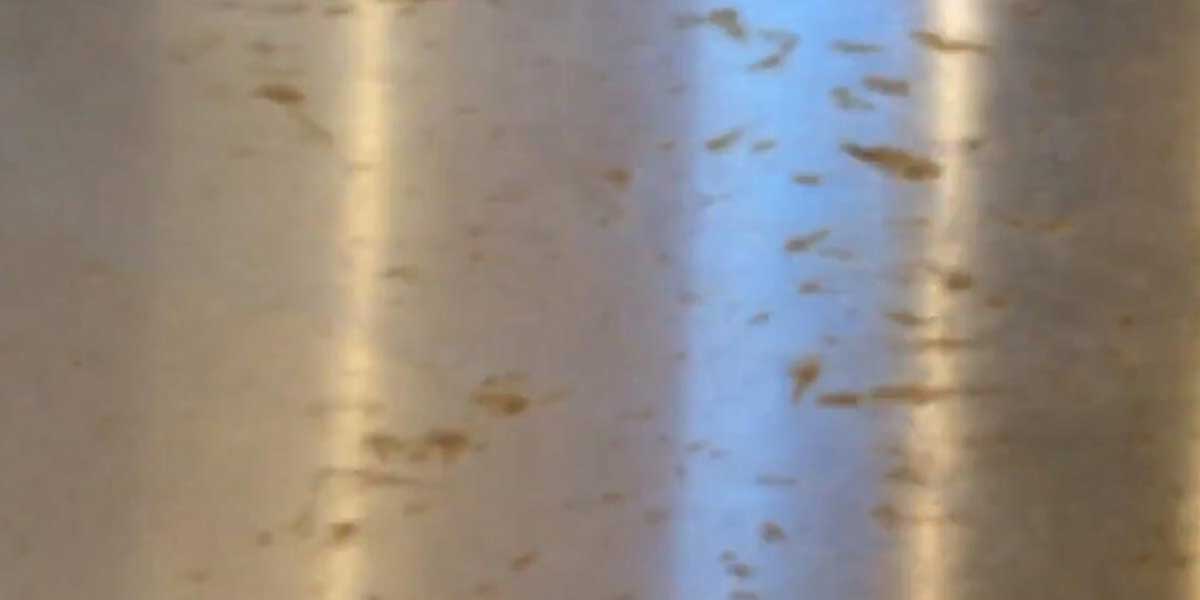
The 316 stainless steel offers high tensile strength.It has a high level of corrosion resistance. Also, 304 stainless steel is very often used in the brewing industries, dairy, food. 304 Stainless Steel Applicationsģ04 stainless steel is commonly used in the kitchen industry. However, like 18-8 grade stainless steel, it is easy to corrosion when exposed to saltwater. It is much easier to mold than 316 stainless steel. It has a high level of resistance to corrosion. The main benefit of 304 stainless steel is usually considered to be one of the strongest of the mild carbon steel available on the market. Advantages and disadvantages of 304 Stainless Steel It also has a strong ability of resistance to the effect of various chemicals and acids. Although it is not easy to rust, it will tarnish. It cannot be heat-hardened and is also non-magnetic. But it is not suitable for marine applications. Ideal for applications in highly corrosive environments, Kitchen equipment, Wheel covers, Storage tanks, Pressure piping and vessels. 18 8 Stainless Steel Applications:ġ8-8 grade stainless steel is used within many different industries. This type of stainless steel is also not only cost-effective but also does not requires maintenance. This does not affect its strength and durability. On the other side,18-8 grade stainless steel properties including goof property of bending and molding. Therefore, it is not the ideal stainless steel to use for marine applications. But, it is still showing signs of corrosion when exposed to chlorides. It can be hardened only by cold working, and it isn’t magnetic.ġ8-8 Stainless Steel Chemical Compositions Chemical Elementįeatures: Non-magnetic,Cannot be hardened by heat treating,Chrome-oxide surface layer,Rust resistant Advantages and disadvantages of 18-8 Stainless Steelġ8-8 stainless steel is famous for its superior corrosion resistance. 18-8 grade stainless steel has better resistance to corrosion than the 400 series. It is available in various appearances and finishes. It is very resistant to corrosion and oxidation, highly durable. It is the most widely used and flexible austenitic form of stainless steel. The common designations include 301, 302, and 304 stainless steel. The rest composition is remainder iron and a dozen or two other elements. Because it contains nominal 18% chromium, 8% nickel. What is 18-8 stainless steel? 18/8 stainless steel is 304-grade stainless steel which is also called 18-8 stainless steel, 18 8 stainless steel. Stainless Steel Casting Foundry and Supplier.What is the conlcusion of difference between 18 8 vs 304, 18-8 stainless steel vs 316 ?.Advantage and disadvantages of 316 Stainless Steel.Advantages and disadvantages of 304 Stainless Steel.Advantages and disadvantages of 18-8 Stainless Steel.

18-8 Stainless Steel Chemical Compositions.If the material is installed architecturally, wash, apply an automotive chrome cleaner/polish and then wax. The contaminants attack the heavily stressed, possibly microcracked material. There may also be some initial contamination from forming or cutting. Very light rainfalls carry surface contaminants to the bottom where they concentrate as the water evaporates. If a large amount of material is involved, consider having a metallurgist or testing lab check whether it meets specifications. A true fix might require annealing + passivation, or may not even be possible if the surface is heavily cracked. Possibly, A554 tubing (A268 & A511 require annealing) or some non-grade stuff. My guess: The fissures suggest cold-worked tubing that is stress corrosion cracking (SCC). Were ordinary steel tools used on the 316, or is there any contact with other metals? How was the tubing cut to length, and were the ends deburred and cleaned thereafter? Passivated? What is causing the SS to rust and how can we cure this problem.Ĭan your furnish photos, including close-ups of the corroded fissures?ĭoes rolling refer to the sheet stock prior to welding into tubular shape, or was some mechanical forming performed on the tubes?Īny specification on the tubing, e.g., ASTM A268, A511, A554.? Rust begins inside these very fine fishers when in contact with rain water. Fishers appear along the bottom rolled edge of our 316 stainless steel tubes. This is the only area of the tube showing signs of rust. What is causing the rolled edge of 316 stainless steel to rust.
